
About Tachi-S
Global Seat System Creator
At Tachi-S, we help automotive manufacturers launch their cars, trucks and SUVs by designing, developing, testing and manufacturing high-quality automotive seats that are functional, safe, stylish and most importantly comfortable.
Each year, Tachi-S delivers over 3 million complete automotive seats and over 4 million seat components to the global automotive market. Our success is based on being responsive, flexible and easy to work with to help assure that every automotive seating program is completed on-time, on-budget and delivered with high quality. That’s how we do business…and that’s why we have been a continuously selected company in the automotive industry.
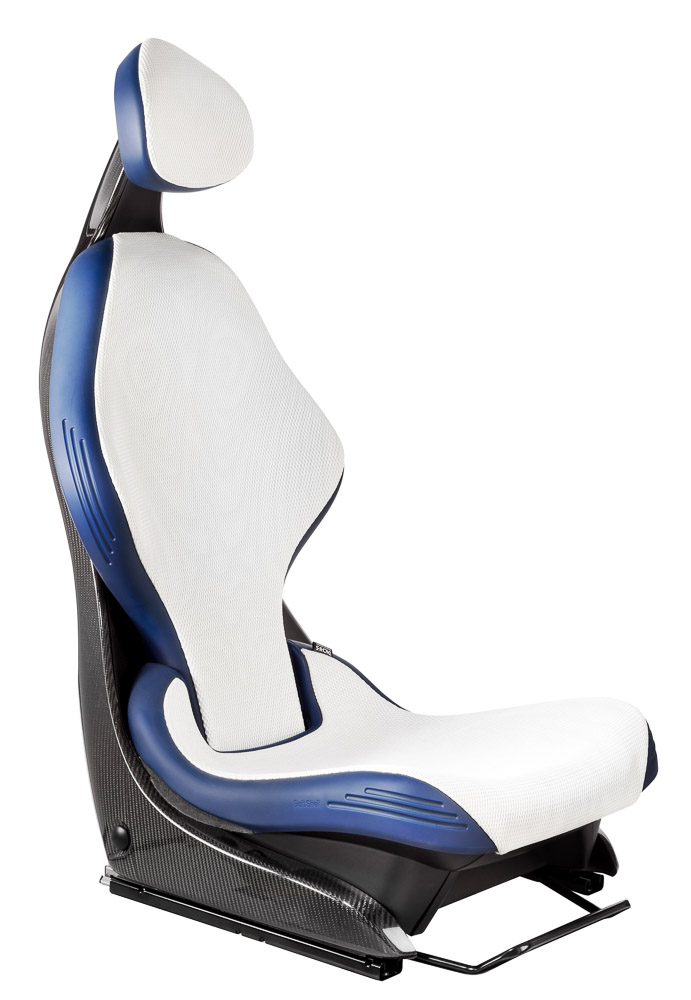
Quality Policy
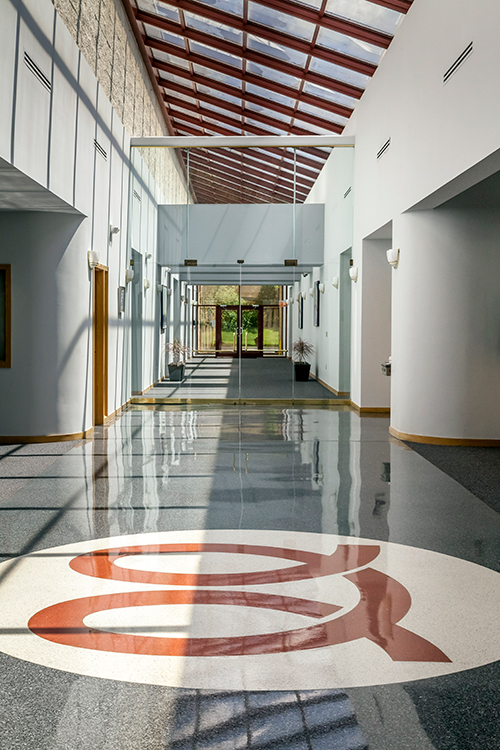
Corporate Philosophy
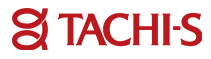