
Job Postings—Mt. Juliet, Tennessee – TEST
Tachi-S Automotive Seating is looking for talented, dependable, hard-working individuals to join our team. We are committed to creating a productive, collaborative work environment while maintaining a healthy work-life balance for our employees.
Current Job Openings
TACHI-S JOB DESCRIPTION
General Job Title: Quality Manager |
Original Date: 3/13/07 |
Department: Quality |
Status: Salaried Exempt |
Revised Date: 6/6/18 |
Basic Functions and Scope of Responsibilities: The Quality Manager provides oversight and accountability for establishing quality policies and programs. Incumbents are responsible for providing inspection and quality expertise to assigned departments to accomplish goals and objectives. The QA Manager establishes overall program design, budget, and staffing forecast. In this role, the manager will seek to continuously improve processes, practices, procedures, and performance in support of Tachi-S objectives. They will analyze reports to determine areas of improvement and the appropriate plan of action and establish and administer the quality policies in line with the corporate guidelines. |
Knowledge/Skills and Abilities (Minimum requirements to perform job): ¨ Excellent leadership and management skills ¨ Excellent interpersonal skills ¨ Ability to manage a variety of cross-functional team members ¨ Excellent written, verbal and presentation communication skills ¨ Excellent organizational and follow-up skills ¨ Competent in problem solving, team building, planning and decision making
Key Responsibilities: ¨ Provide clear leadership for the development of an environment focused on Quality. ¨ Develop quality-process links with customers in line with the Quality Management system (including: IATF16949, ISO14001 / ISO 9001 / OHAS 18001) Production Part Approval Process (PPAP), Advanced Product Quality Planning (APQP), Controls Plans, Failure Mode and Effect Analysis (FMEA) and Supplier Quality Assurance (SQA) processes and oversee continued compliance and embedding across the business. ¨ Responsible for maintaining relationships with customers and suppliers to maximize profit potential and ensure efficiency. ¨ Manage the audit program as well as supplier development and improvement ¨ Play a key role in ensuring project deliveries. ¨ Work proactively with all managers, supervisors, and employees to maintain a program of continual improvement within their areas of responsibility. ¨ Lead a “correct at source” and problem-solving methodology (Lean). ¨ Lead the team to achieve quality targets for customers and business goals. ¨Specific Duties: Strategy and Development ¨ Contribute to the creation and implementation of best practice quality ¨ Vision, strategy, policies, processes, and procedures to aid and improve operational performance ¨ Contribute to new business initiatives and projects and review and communicate the impact on Quality activities General and Task Management ¨ Implement all relevant procedures described in the Quality Management System (QMS) and ensure compliance ¨ Ensure that all in-house systems and procedures are updated, revised, and modified to meet the needs of external certification bodies ¨ Respond to customer complaints putting in containment actions, full analysis, poka-yokes (error proofing), and implementing short-term and long-term countermeasures ¨ Champion a program for the implementation and sustainment of a continuous improvement culture ¨ Act as a point of contact for warranty issues ¨ Update quality documentation and communicate to carry forward lessons learned from quality concerns in new customer contracts ¨ Ensure that all necessary systems and procedures are in place to satisfy all customer requirements and audits ¨ Introduce new systems and procedures where appropriate ¨ Train others in all aspects of the quality system and application of procedures ¨ Undertake internal and process audits of the Quality Management System (QMS) ¨ Management of the Quality Engineers and Technicians in the sign-off of parts and the resolution of internal/external quality concerns ¨ Establish and refine quality sign-off instructions, standards, and documentation ¨ Report against agreed quality metrics on a monthly basis ¨ Lead regular inspection meetings with representatives from appropriate departments to establish an action plan for improving build quality ¨ In conjunction with the Supplier Quality Assurance function, reduce the effect of non-conforming supplier materials on the production area quality ¨ Attend various meetings and action/communicate instructions ¨ Produce written reports and make presentations ¨ Undertake continuous training and development ¨ Perform root cause analysis and resolve problems ¨ Stay current and up to date on any changes that may affect the supply and demand of needed products and materials and advise others of any impact ¨ Identify business improvement opportunities within the organization ¨ Identify and deploy the technical skill sets, resource levels and systems to deliver projects, including the engagement of external resources as required ¨ Develop, implement, and manage key performance indicators (KPIs) for each area of responsibility ¨ Set department objectives/KPIs and review and assess ongoing performance of direct reports ¨ Ensure KPIs are met by working to the overall plan, including management of, and reporting ¨ Report on achievement of targets and identify any actions required ¨ Ensure that the function operates in accordance with any health, safety and environmental policies and procedures to ensure the safety and wellbeing of staff and visitors ¨ Conduct risk assessments of processes and tasks in the department People Management ¨ Ensure the delivery of the team within each area of accountability ¨ Manage, coach, and develop a high performing Quality Operations team that meets agreed objectives, and which delivers best practice results, added value and continuous improvements ¨ Manage and lead the team, ensuring adequate staffing levels ¨ Motivate and coach the team to operational success ¨ Monitor the completion of tasks and ensure good performance and record on appropriate systems ¨ Consistently promote high standards through personal example and roll out through the team so that each member of the team understands the standards and behaviors expected of them ¨ Review, implement, and update company records e.g., training matrices, performance reviews, risk assessments ¨ Communicate KPIs from the strategic annual plan so that each employee is aware ¨ Provide technical expertise to the team ¨ Manage contractors on site to ensure they meet legal and company requirements Relationship Management ¨ Develop and maintain strong relationships with internal and external stakeholders to ensure optimal performance ¨ Work collaboratively, negotiate and engage with key stakeholders to facilitate delivery and compliance with the Quality strategy ¨ Communicate with stakeholders the impact of market change and potential effects on engineering design and development. Recommend solutions without compromising quality or service while optimizing cost ¨ Liaise with suppliers to resolve quality issues ¨ Liaise and communicate with other departments, customers, suppliers, and other service providers ¨ Work as part of the Management team to share ideas and improve operation, recommending, supporting, and implementing continuous improvement activities and process and procedure improvements to optimize results and improve quality of delivery, in line with quality standards requirements delivery in line with Company and Customer requirements ¨ Communicate with personnel at all levels, internally and externally to the Company, in relation to Quality matters
|
|
||
Education Requirements: Check the minimum level of formal education that is required to perform this job satisfactorily. |
Additional Qualifications/Experience Preferred: · Membership of an industry related professional organization · Experience in high volume manufacturing environment – automotive preferred · 4-7 years’ experience in Quality\ · Six Sigma/Lean Manufacturing Skills |
|
High School Diploma or GED Preferred |
|
|
Vocational School or some college courses |
|
|
Associates Degree, Trade or Technical School |
|
|
Bachelor’s Degree (Engineering Major) |
X |
|
Physical Effort: |
_____X_____ Minimal |
__________ Moderate |
__________ Substantial (List Examples) |
Sensory Attention: |
__________ Minimal |
_____X_____ Moderate |
__________ Substantial (List Examples) |
Approvals:
I have reviewed the job description and understand the requirements of the position. A copy of this description will be provided to the employee.
|
|
|
Tachi-S Automotive Seating provides equal employment opportunities to all employees and applicants without regard to race, color, religion, sex, national origin, age, disability, height, weight and marital status or status as a Vietnam-era or special disabled veteran in accordance with applicable federal and state laws. This policy applies to all terms and conditions of employment, including but not limited to: hiring, placement, promotion, termination, layoff, recall, transfer, leave of absence, compensation and training.
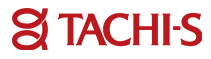